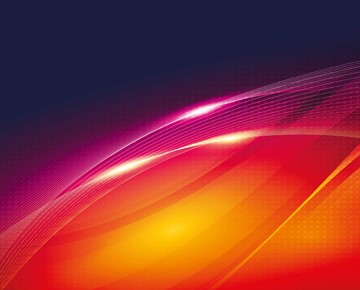
Thermal Management Applications
Advanced thermal management solutions using high-performance materials
Development of an OEM approved framed thermal cell barrier to delay thermal runaway in Electric Vehicle battery packs
“We regularly work with large OEMs but this project was a real milestone for Tecman. The whole company ended up being involved in supporting this project in one way or another, from design support and technical teams to logistics and operations.
Our engineers helped to develop an exceptional solution that surpassed the customer’s expectations and has led them to make significant investments into the manufacturing machinery for our solution.”
Kevin Porter, Tecman's Managing Director
Who did we work with?
We recently undertook a project with a major automotive OEM. They approached Tecman in 2021 to help with the design and manufacture of a thermal cell barrier to better manage thermal runaway within EV battery packs.
What was the project?
A major automotive OEM approached us with a challenge that required significant support with design and materials.
At a basic level, they needed a concept-to-manufacture solution that would enable them to prevent thermal propagation between neighbouring battery cells in their electric vehicle (EV) range and meet the global requirement of a five-minute delay before thermal runaway occurs.
Tecman were able to use our in-house expertise to accelerate product development. As a materials specialist and proven automotive manufacturing partner with extensive experience of producing thermal management solutions across industries, we stood out and were well placed to help them identify, select and design a solution to this challenge.
The solution needed to meet a comprehensive specification, which evolved as the project progressed. Tecman collaborated closely with the customer, providing end-to-end support to develop a solution.
What did we do?
Tecman’s engineers drew on their extensive materials knowledge and application experience to identify several potential materials that would be suitable for the purpose of insulation and shortlisted three of these for further testing and investigation. This included aerogels and ceramic fibres, ensuring at all points that they were suitable for high volume manufacturing and met compression and fire-retardant requirements.
As the design of the thermal cell barrier evolved, it became clear that a controlled space between each cell was required, necessitating the introduction of a frame. Our team also explored various solutions options like extrusion down the edges of the cell barrier, but a full framed solution emerged as the more effective solution to this challenge.
In the first instance, the design of the frame focused on a two-part system that clipped together and mechanically held the insulation component in place. Customer simulations indicated adhesive would be required on both faces around all four edges, and we carried out trials and produced prototype parts to validate this theory.
Two challenges that emerged during this process. CAD designs did not translate to physical structures as anticipated, due to the flexibility of the final selected material. Assembly testing then revealed issues with the connection action of the two-part frames proving to be slow and cumbersome.
The Tecman team took a step back, re-evaluated different designs and explored modifications to the original design. This included looking at a single part frame with the adhesive covering the whole face of the part, encapsulating the insulation material within the frame. This framed solution provides critical mechanical support to the battery cells and gives them space to expand and contract, maximising the cell life and providing the most effective thermal barrier.
What did we achieve?
The customer needed a solution for managing thermal propagation that was also suitable for high volume manufacture, and was open to support and advice on how to identify, develop, test and mass produce a solution.
We used our engineering, manufacturing and consultancy expertise to advise the customer and collaboratively design an exceptional solution for them that was suitable for high volume manufacture and that kept sustainability concerns at the forefront of design choices. Our engineering knowledge enabled us to bring a ‘big picture’ perspective to the project that helped the customer team to consider a variety of solutions that were aligned to a low-cost, high-volume manufacturing strategy.
The Tecman team worked closely with the customer’s engineering team over the 18-month project, maintaining constant contact and developing a strong relationship based on trust and expertise. We provided design and engineering support on a weekly basis through a scheduled project meeting, and our recommendations were seen as a source of added value.
This led to the design of a Framed ATP Pad solution, which is being used by the customer across their EV range and has resulted in them investing millions of pounds in the new equipment and machinery necessary to manufacture this design. It increased the thermal propagation delay to over 20 minutes, significantly exceeding the five-minute global standard and meeting the major requirement for the project. The whole team were delighted with the service Tecman provided and have continued to work with us on other projects.
Our value is as an end-to-end partner that brings extensive cross-sector materials expertise and understands how to support the design of thermal management components for high volume manufacture.
The customer used Tecman as an adviser on different areas of design and material selection, to collaboratively design a product that met all key requirements. Our ability to recommend materials used in other industries added huge value, and they continued to consult us post-project, making the most of our excellent post-sales support.
For applications that require thermal management, such as battery cells, battery packs, and electronic components, we develop comprehensive end-to-end thermal management solutions by working in collaboration with our customer partners. From conceptualisation to production, through to ongoing engineering support, we deliver solutions that solve industry challenges, enhance performance and safety of the end product and exceed project expectations.
Framed ATP Pads are an advanced thermal cell barrier with built-in spacers for prismatic cells designed to delay or prevent cell-to-cell thermal runaway.
Encapsulated ATP Pads are an advanced thermal cell barrier for pouch cells that delay or prevent cell-to-cell thermal runaway.
Sekisui thermal interface materials for advanced thermal transfer solutions between EV battery components.
Ultra-lightweight insulation materials with the highest thermal insulation to weight value of any material.
A range of thermal transmission grade acrylic foam tapes precisely formulated to provide semi-structural bonds on various substrates whilst aiding thermal transmission.
Thermal management natural and synthetic graphite materials can be converted into complex die-cut parts to provide thermal interface and bonding properties; reducing hot spots and protecting sensitive components.
A range of specialist thermally conductive adhesive-backed metallic foil tapes including aluminium, copper, embossed and tinned copper with various adhesives, finishes and conductive properties.
Advanced thermal management solutions using high-performance materials
Effective thermal runaway barriers are essential for optimising cell performance, longevity, and saf…
Within the ever-evolving and dynamic e-mobility sector, Tecman is a trusted and proven partner to un…
Thermally conductive acrylic foam tape has been designed to offer superior transfer of heat for LED…
Tecman’s engineers have spent the last 18 months developing a process that enables the high volume,…
After showcasing our advanced thermal runaway barriers at The Battery Show Europe, we share the freq…
6 key insights from our conference session at Battery Cells & Systems Expo, titled 'Delivering Cost-…
Our proven track record underlines our commitment to delivering value-added products with consistent…