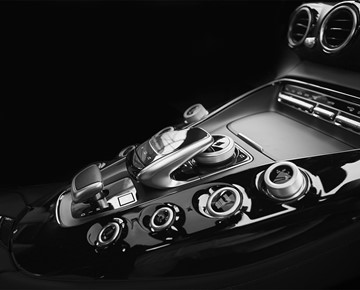
Case Study: OEM Approved Protection Film
Developed a solution with a major automotive OEM to protect piano black paint during manufacturing p…
Development and manufacture of an adhesive gasket to bond a curved plastic component to a vehicle instrument cluster
"The customer was very engaging to work with and their engineers bought into our designs, appreciated the engineering support that we offered and listened to the recommendations we made.
This collaborative working approach enabled the project to become a real success and has enabled the component to pass the stringent specification of a leading automotive manufacturer.”
Wayne Matthews, Tecman's Project Lead
A leading manufacturer of high-quality functional plastics for a range of industries approached Tecman to help with the design and supply of an automotive die-cut solution for a high-profile OEM.
Our customer needed a precision die-cut adhesive gasket that would enable them to bond their component onto a vehicle instrument cluster. As a materials specialist and proven automotive manufacturing partner, we were well placed to deliver a value-add solution.
Like Tecman, the customer plays an important role in a long and complex supply chain, so the gasket needed to be able to be applied contact-free by the customer, and the backing liner would need to be removed later in the supply chain by their customer.
We approached this project from first principles. Our engineers took time to understand the customer’s objectives and technical requirements before designing a bespoke precision die-cut solution that met the specification and budget for the project.
The Tecman team designed a double-sided 100µm thick die-cut adhesive gasket that could bond their component to a vehicle dashboard. As part of this, we included dry finger tabs at two points to prevent contamination of the adhesive during placement and liner removal – a key customer requirement.
We then began testing and trialling the solution on the customer’s components. As often happens during prototyping, testing revealed several challenges and highlighted opportunities to refine the product and improve.
Firstly, we identified a need for a light blocking adhesive to prevent the end product providing confusing visual information to the driver.
This added complexity to the project, but the team addressed this by working with the customer to narrow down their specific requirements and used our design expertise to recommend appropriate solutions that remained within the scope of the project.
This led to a re-engineering of the part and the selection of a unique adhesive product that would block light transfer between each icon in the component.
Secondly, we identified and remedied potential issues with the application of the gasket consistently onto the compound angles of the customer’s component. The gasket struggled to stretch under tension, resulting in the adhesive lifting off the substrate and causing tenting in the corners.
Maintaining a consistent application was a challenge our customer had faced previously, so we recommended that the gasket included relief cuts to allow the adhesive to relax and fit snugly into the concave shaped component.
Our customer came to us knowing they needed a die-cut automotive adhesive gasket, but not knowing what the final solution would look like.
We were able to use our design & engineering support, and consultancy expertise to provide a full end-to-end service, from scoping requirements through to high-volume manufacture, guiding the customer through the design process and drawing attention to the need for modifications on the original concept. This design and engineering support was appreciated, and our recommendations were seen as a source of added value.
The product we supplied is being used by the customer as a component in the OEM's vehicles. Tecman components have had widespread use in automotive vehicles for many years, and this project was an excellent example of a cross collaborative approach. The whole team are proud of the small but vital role we played in helping create an effective, safer vehicle.
Our value lies in being an end-to-end partner, offering both consultancy expertise and manufacturing capabilities.
In this project, the customer engaged Tecman as an adviser on various design aspects, leveraging our multisector expertise to engineer a solution that evolved from the original concept and surpassed expectations.
Our role as both an adviser and a manufacturer in this automotive die-cut adhesive gasket project is not unusual. Businesses are increasingly turning to Tecman because we add value beyond manufacturing existing designs. We bring experience, expertise, and knowledge to projects, working seamlessly with in-house teams to refine and improve concepts.
We support our customers through every stage, from complex material selection and design phases to choosing the right manufacturing processes. This ensures the delivery of an optimised, cost-effective solution designed for high-volume production.
If your application could benefit from cost savings, process improvements, material enhancements, and product advancements, reach out to a Tecman expert to discover how we can support your application.
Developed a solution with a major automotive OEM to protect piano black paint during manufacturing p…
We manufacture custom die-cut adhesive tape and engineered adhesive tape solutions
As a trusted automotive partner, we work with OEMs and tier suppliers across the globe to develop ad…
Customised automotive adhesive tape solutions that are engineered to withstand all environmental con…
We have the flexibility to convert all our industrial double-sided adhesive tapes into customised so…
The interior trim of a car is critical for completing the sense of style established by the exterior…
The demand for enhanced performance, improved passenger comfort and safety, and lower carbon emissio…
Our proven track record underlines our commitment to delivering value-added products with consistent…